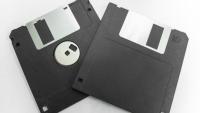
While many have transitioned away from using floppy disks, there are moments when we need to access older information stored on them. However, in doing so, a series of issues may arise. You might encounter messages like:
A:\ is not accessible. The device is not ready. Disk is not formatted. Do you wish to format it now? STOP: The disk media is not recognized; it may not be formatted. Interestingly, these problematic disks may function correctly when used with older operating systems like MS-DOS or Windows 95.
Root of the Issue
The main culprit behind these issues is the absence of a media descriptor byte in the BIOS parameter block (BPB) found in the boot sector of the floppy disk. Historically, many preformatted floppy disks, especially older ones, lacked this media descriptor byte.
The role of the media descriptor is vital as it identifies the type of medium present in a drive. Whereas systems like MS-DOS and Windows 95 didn't require the setting of this byte, modern systems do, which is why we see these compatibility issues arise.
Efficient Solutions
Reformatting: The most straightforward solution is to reformat the floppy disk using newer versions of Windows such as Windows 98 or XP. By doing this, the system ensures the necessary media descriptor byte is present. Advanced Workaround: For those who are tech-savvy and understand the risks involved, there's an advanced workaround. By using a disk sector editor, one can modify the media descriptor byte on the floppy disk. A word of caution: misuse can lead to permanent data loss, so proceed with the utmost care. Tools like DiskProbe (Dskprobe.exe) — included in Windows Support Tools for systems like Windows XP Professional — can be employed for this purpose.
Understanding Media Descriptor Bytes
To delve deeper, here are some common media descriptor bytes:
F0: Represents 2.88 MB on a 3.5-inch, 2-sided, 36-sector, or 1.44 MB on a 3.5-inch, 2-sided, 18-sector disk. F9: Used for 720K on a 3.5-inch, 2-sided, 9-sector disk, and 1.2 MB on a 5.25-inch, 2-sided, 15-sector disk. FD: Denotes 360K on a 5.25-inch, 2-sided, 9-sector disk. And so on... These bytes are located in sector 0 of the disk, providing a hint about the media type and its compatibility.
Final Thoughts
The evolution of technology means some older storage mediums become challenging to access with newer systems. By understanding the root of these compatibility issues and knowing the ways to circumvent them, we can ensure the preservation and access of valuable data, even from antiquated storage methods like floppy disks.
- ms-dos
- data accessibility
- disk sector editor
- windows compatibility
- disk formatting
- floppy disk
- bios parameter block (bpb)
- data recovery
- media descriptor byte
- diskprobe
- legacy storage solutions
- windows 95
- Read more...
-
- 0 comments
- 1,748 views