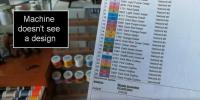
Olga approached the embroidery machine. In her hand, there was a brand new 32 Gb USB flash drive that she had bought online specifically for the purpose. Olga drew her breath. She was about to initiate her very first contact with the embroidery machine. Olga stretched her arm in the direction of the USB port on a side panel. The data transfer was about to commence!
Her swift stylus was flying over the screen, guiding her to the location, which, according to the manual, contained her embroidery designs. These operations were familiar to Olga: after all, she didn’t play Solitaire on her phone during the long winter evenings for nothing. In the end, she was in for a disappointment: the machine found no designs on the USB flash drive. Olga was quite puzzled: what happened to her files and why the machine did not see them?
The embroidery machine doesn’t recognize a design
This article deals with the problems almost every machine embroidery novice encounters sooner or later. Gradually, old problems are solved and give way to the new ones; therefore, the information accumulated here will be updated.
Before loading the designs into your embroidery machine, carefully read the manual to learn how this can be done. Presently, the most popular way of doing that is using a USB flash drive. For this very reason, it is the USB Flash drive that is most troublesome for novice embroiderers.
In this article, I’ll describe the main reasons for the design load failure, together with the possible solutions.
The stitch file format is unfamiliar for your embroidery machine
The embroidery machine manual always lists all compatible file formats/types. The format/extension is identified by the three letters after the dot in the name of the file.
Every manufacturer has its own format to add to the embroiderer’s troubles.
Brother — PES Janome — JEF Bernina — ART Pfaff — VIP And so on.
If you saved your design in the PES format, and your machine can only read JEF and DST, do not expect miracles. Your machine won’t be able to see the design.
Today, DST is considered a universal stitch format. A lot of manufacturers are aware of the fact, their equipment supporting both DST and the format that is its “native”.
If your machine can read DST — use it!
USB flash drive is full
You have crammed too much information into your USB flash drive. This problem does not occur frequently, but it might, especially if you own a machine of one of the previous generations. Try to format the USB flash drive and then load the designs. If the solution has worked, congratulations! If not, read on.
You’re using a file format of the newer version
I've mentioned the file formats/types just above. You already know that your machine supports PES files, but the machine still fails to recognize them. One possible explanation is that you’re using a newer version of PES than the ones supported by your machine (there are approximately 10 versions of it in total). This trouble usually bothers the owners of the machines that support PES format. What can be done in this case?
Open the file in any converter software and save it in the older version of the format. Embird automatically saves the files in the latest version of the format, it being compatible with the majority of Brother embroidery machines.
Machine embroidery design was saved to a wrong folder
Again, I suggest perusing your embroidery machine manual. It describes the correct sequence, in which the designs should be saved to the USB flash drive, and how to prepare it for the task. Before starting to load any designs, you should format it. Switch on your embroidery machine and insert your USB flash drive into the port. The machine will find and format it, if necessary, creating the system folders. It is in one of these folders that the files should be loaded.
In case your machine was made after 2014, you’ll most probably never have to face this problem, as the loading process has since been simplified. On the other hand, anything can happen.
The design is too big
Any embroidery machine has a maximum embroidery area. It determines the largest size of the design that can be loaded into this particular piece of equipment. If you try to load a 141x139 mm design into the machine that only handles the ones up to 140x140 mm, it won’t be recognized. Open the design in any converter/embroidery editor and check the size. If the design is too large, resize it without stitch recount so as to preserve the decorative fills.
P.S. Do not mistake the Giga hoop size with the maximum embroidery area!
Embroidery design is not centered
Some embroidery formats contain information about the positioning of the design along the X and Y axes. They convey this information to the embroidery machine, and, in case the design is off-center, the machine will fail to recognize it. This problem can be solved by using more complex converters or software specifically designed for the loading of the designs into the embroidery machine. As a rule, they center the designs automatically.
P.S. This trouble is common for Janome embroidery machines, with their native JEF format. The ultimate fix is provided by Customizer or Embird. Convert the design, ticking the Center in the Hoop box.
You forgot to load the design to the USB Flash drive
Yep, it happens. Insert your USB flash drive in the port on your laptop or PC and check.
Stitch count is too large
This problem usually occurs on the old machines with small hoops, when one is trying to embroider PhotoStitch designs on them. It means the embroidery file contains more stitches that the machine can process. Solution: divide the file by color into two parts.
USB flash drive is not compatible with the machine
A home embroidery machine is a whimsical lady: sometimes the size is all wrong, sometimes it is the face (or, rather, the manufacturer) she takes an immediate dislike to. If nothing of the above has helped, get a new USB flash drive. Which one to choose? I won’t recommend any particular brands. In my experience, two machines of the same manufacturer and of the identical version treated the same USB flash drive differently: one easily recognized all files, the other refused to do it until they were saved in the special design loading software. Furthermore, the machine behaved in a strange way, stitching like there’s no tomorrow, once the USB flash drive was inserted. So, seek your own USB Flash drive, and ye shall find.
Choose the smaller one. The smaller, the better.
If you have any questions or suggestions, please feel free to write us a commentary or start a topic in the community. May only the easy-to-read formats and universally accepted USB flash drives come your way!
Original text by Lisa Prass
- Read more...
-
- 3 comments
- 7,904 views